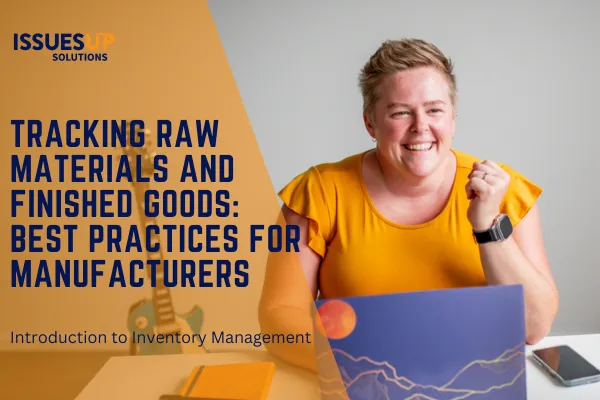
Tracking Raw Materials and Finished Goods: Best Practices for Manufacturers
Tracking Raw Materials and Finished Goods: Best Practices for Manufacturers
In the world of manufacturing, effective inventory management is crucial for maintaining operational efficiency and meeting customer demands. A well-organized inventory system distinguishes between raw materials and finished goods, ensuring that each stage of the production process is seamlessly integrated. This blog post will cover best practices for tracking raw materials and finished goods and highlight the importance of creating categories for inventory.
The Importance of Categorizing Inventory
Categorizing inventory creates a structured framework for all inventory-related activities. By classifying items into clear categories, manufacturers can:
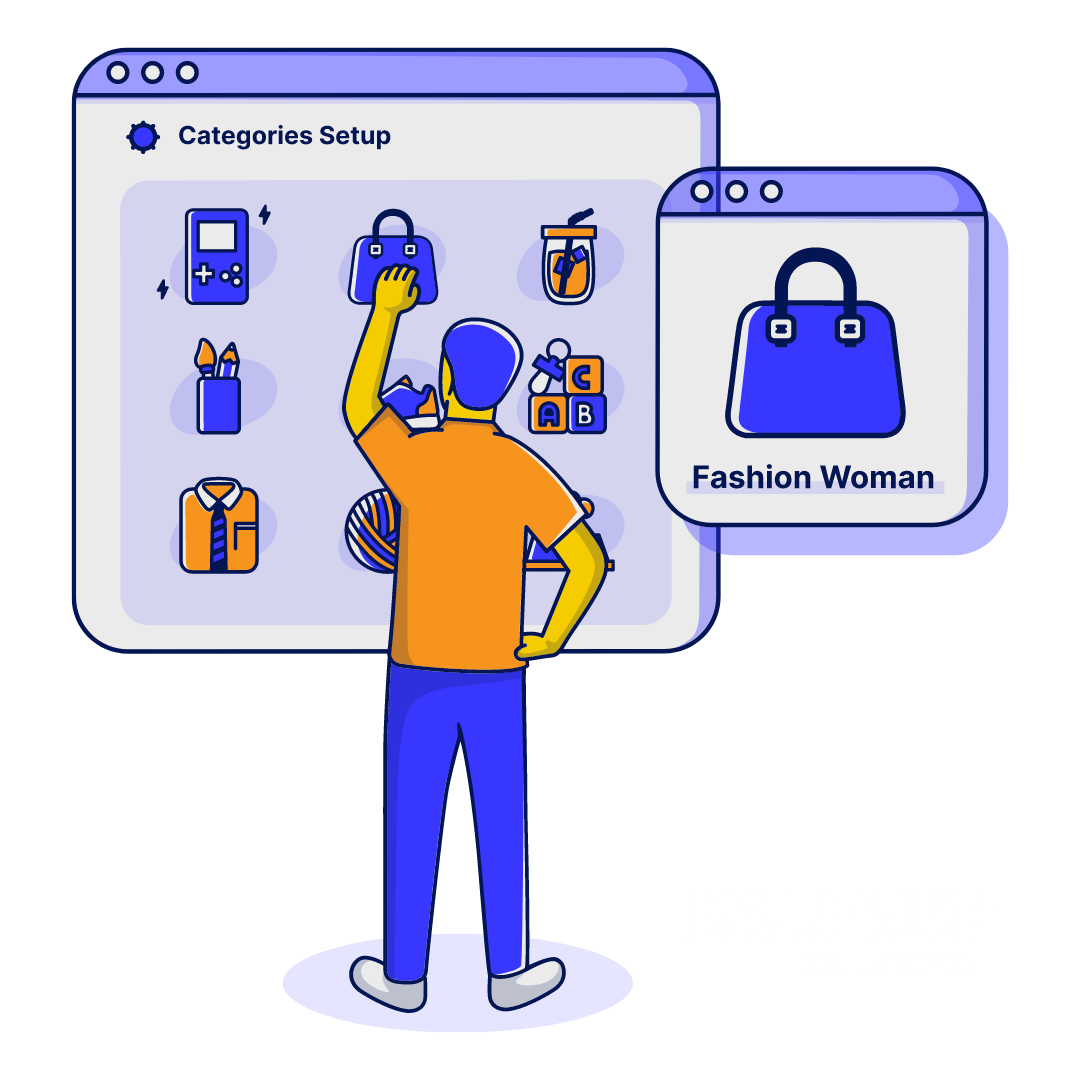
Improve Accuracy: Consistent categorization reduces errors and makes it easier to track
quantities and locations.
Enhance Forecasting: Understanding the levels of various categories helps in making more accurate demand forecasts and production schedules.
Streamline Operations: Organized inventory enables a smoother flow through the production process, minimizing disruptions and delays.
Optimize Storage: Efficient categorization helps in optimizing warehouse space and improving access to essential items.
Not only is it important to categorize inventory as finished goods and raw materials, but it is good to have categories withing those categories. For instance, within the raw materials category, you could split it out into corrugated, bags, labels, ingredients, etc. For finished goods, you could split them out by form or by main ingredient. Do what works best for your manufacturing facility. By categorizing your inventory, you can use those categories to dig into each area of inventory. Patterns may start to emerge, like why do I have 30 different box sizes? Can I consolidate sizes and reduce my overall inventory?
Best Practices for Tracking Raw Materials
Implement Barcoding/RFID Systems: Use barcode or RFID technology to track raw materials. These systems provide real-time updates and reduce manual errors. This is if your current system can support barcode scanning capabilities.
Regular Audits and Cycle Counting: Like I mentioned last week, perform regular audits and cycle counts to ensure accuracy. Schedule counts for high-value or frequently used materials more often.
Supplier Management: Maintain good relationships with suppliers to ensure timely deliveries and quality control. Implement a system for tracking lot numbers and expiry dates.
Inventory Management Software: Utilize specialized software to manage raw materials. Look for features like automatic reordering, real-time tracking, and integration with other systems.
Setting Reorder Points: Define minimum stock levels for each raw material and set reorder points to avoid stockouts and overstocking.
Best Practices for Tracking Finished Goods
Labeling and Barcoding: Label all finished goods with unique identifiers. Barcoding finished products aids in tracking their movement and location.
Separate Storage Areas: Designate specific storage areas for finished goods to prevent confusion with raw materials. Clearly label shelves and bins. In food and beverage facilities, this is essential especially in regards to allergens or cross contamination.
First-In, First-Out (FIFO): Implement FIFO methods to ensure that older inventory is used or shipped first, reducing the risk of obsolescence.
Inventory Reconciliation: Regularly reconcile finished goods inventory with sales and production records. This helps in identifying discrepancies and resolving them promptly.
Integrated Systems: Use integrated inventory management systems that connect production, warehousing, and sales. This ensures consistency and real-time visibility across departments.
Bridging the Gap: From Raw Materials to Finished Goods
Transitioning raw materials into finished goods is a critical phase in the manufacturing process. To maintain efficiency:
Track Work-in-Progress (WIP): Use systems to monitor WIP inventory, ensuring that semi-finished goods are efficiently processed to completion.
Batch Processing: Schedule production in batches to streamline the transformation from raw materials to finished goods, reducing setup times and improving throughput.
Quality Control: Implement robust quality control measures to inspect raw materials and finished goods, ensuring that standards are met at every stage.
Conclusion
Effective tracking of raw materials and finished goods is essential for any manufacturer aiming to improve efficiency, reduce costs, and enhance customer satisfaction. By adopting best practices and creating structured categories for inventory, manufacturers can achieve greater visibility and control over their entire supply chain.
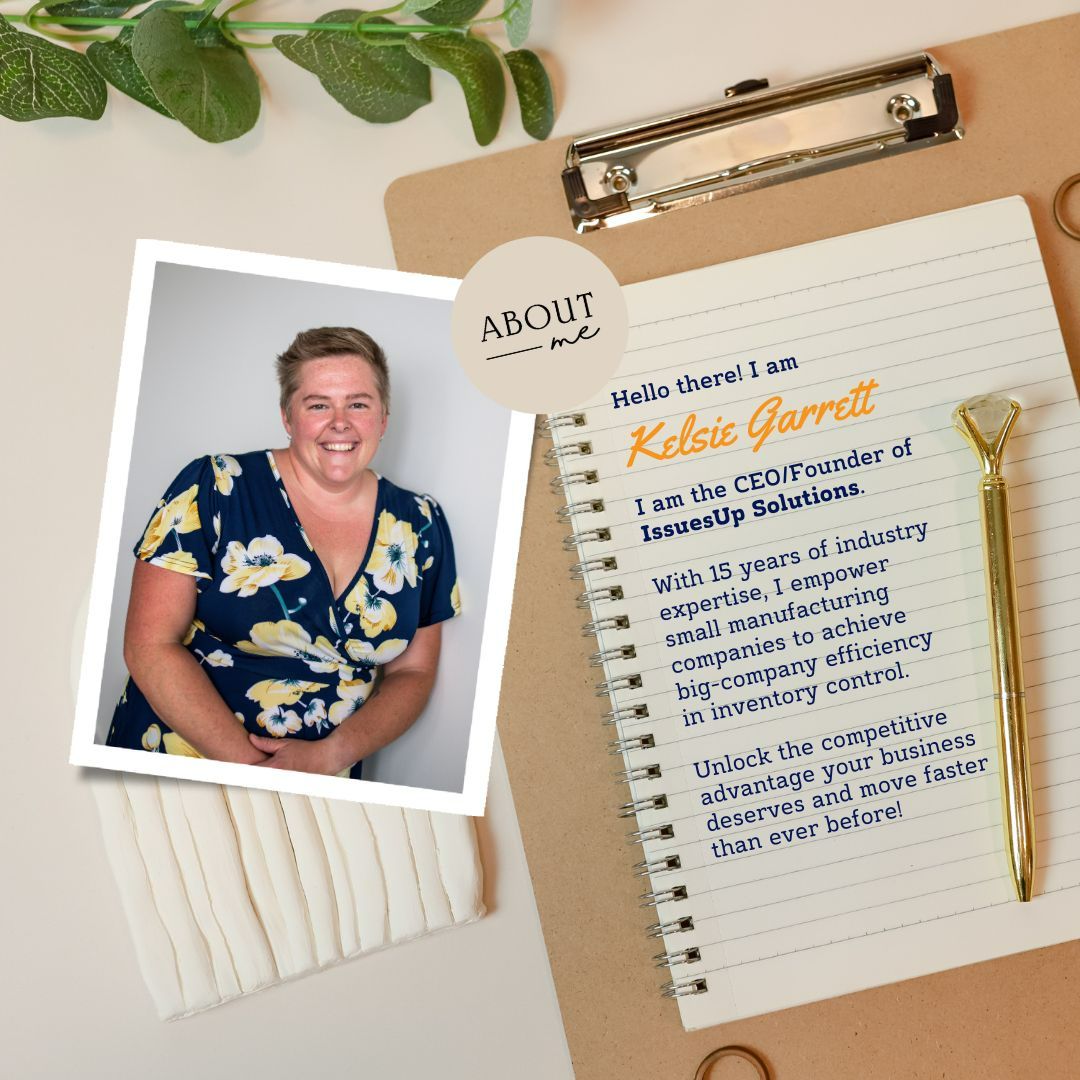