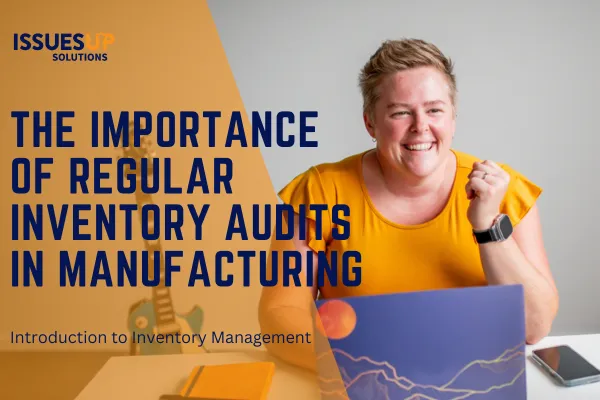
The Importance of Regular Inventory Audits in Manufacturing
The Importance of Regular Inventory Audits Manufacturing
When it comes to managing your business, few things are as critical as maintaining an accurate inventory. The key to achieving this lies in regularly conducting inventory audits. These audits play a vital role in ensuring that your inventory records are accurate and that your business operations run smoothly. In this post, we’ll explore the importance of inventory audits and how they can benefit your business.
What is an Inventory Audit?
An inventory audit is a systematic process of checking the stock you physically have against your inventory records. This involves counting physical inventory, verifying records, and ensuring that everything matches up. Regular audits help identify discrepancies due to theft, loss, damage, or administrative errors. Without accurate inventory, you might as well flip a coin each day to decide what product to produce.
Why Are Inventory Audits Important?
1. Accuracy in Financial Reporting:
Accurate inventory records are essential for precise financial reporting. Inventory affects various financial metrics, such as cost of goods sold (COGS), net income, and profitability. Regular audits help ensure that your financial statements reflect the true value of your inventory, providing a solid foundation for financial decision-making. Make sure that you involve your accounting department when conducting an inventory audit so they can understand and explain any variations in inventory value before and after the audit.
2. Improved Inventory Management:
Conducting regular audits helps you track inventory levels accurately, preventing overstocking or stockouts. This allows for better demand forecasting, more streamlined operations, and efficient use of storage space. By staying on top of your inventory levels, you can make informed decisions about purchasing and production. This will almost completely stop the back and forth chatter about not being able to make something due to the material being missing or misplaced.
3. Identifying Shrinkage:
Shrinkage, or the loss of inventory due to theft, damage, or administrative errors, can significantly impact your bottom line. Regular audits help identify the sources of shrinkage, allowing you to implement measures to prevent future losses. This could involve tightening security, improving storage conditions, or enhancing employee training. Inaccuracies in regards to shrinkage can also be a sign of issues with your bills of materials or how production accounts for ingredient usage during production.
4. Enhanced Customer Satisfaction:
Accurate inventory records ensure that you can fulfill customer orders promptly and accurately. Nothing frustrates a customer more than receiving the wrong item or facing delays due to stockouts. If you use an external warehouse, it can also reduce the frustration for them having to tell you something doesn’t exists in their warehouse. By conducting regular audits, you can minimize these issues, leading to higher customer satisfaction and loyalty.
5. Compliance with Regulations:
For certain industries, maintaining accurate inventory records is not just good practice—it's a legal requirement. Regular audits ensure compliance with industry regulations and standards, helping you avoid potential fines and legal issues.
How to Conduct an Effective Inventory Audit
1. Plan and Schedule:
Set a regular schedule for conducting audits, whether it's quarterly, monthly, or annually. Planning ahead ensures that you're adequately prepared and that audits become a standard part of your business operations. You do not need to count every item every time you conduct an inventory audit. I suggest conducting monthly audits on 10-15% of your inventory so that over the course of the year you count each item at least once over the course of the year.
2. Use Technology:
Leverage inventory management software and barcode scanning to streamline the audit process. Technology can help reduce human errors and make the auditing process more efficient.
3. Involve Your Team:
Ensure that your team understands the importance of inventory audits and is trained in the procedures. Getting everyone on board promotes accountability and helps maintain accurate records. Recruiting team members from other areas to audit helps get fresh eyes on the inventory and prevents assumptions from being made.
4. Review and Act:
After completing the audit, review the findings and take corrective actions as needed. Address any discrepancies, update your records, and implement measures to prevent future issues. An acceptable percentage of errors for an inventory audit typically falls between 1% to 2%. This range is considered a good benchmark for most industries, though it can vary depending on the nature of the business and the complexity of the inventory system. If you are starting out, this number may be higher and may indicate the need for a more comprehensive audit to correct the inventory.
Conclusion
Inventory audits are an indispensable part of effective inventory management. They ensure accuracy in financial reporting, improve inventory control, identify shrinkage, enhance customer satisfaction, and ensure regulatory compliance. By making inventory audits a regular practice, you can maintain accurate records and drive your business towards success.
Remember, the key to efficient inventory audits is consistency and attention to detail. So, mark your calendar, gather your team, and make inventory audits a priority for your business!
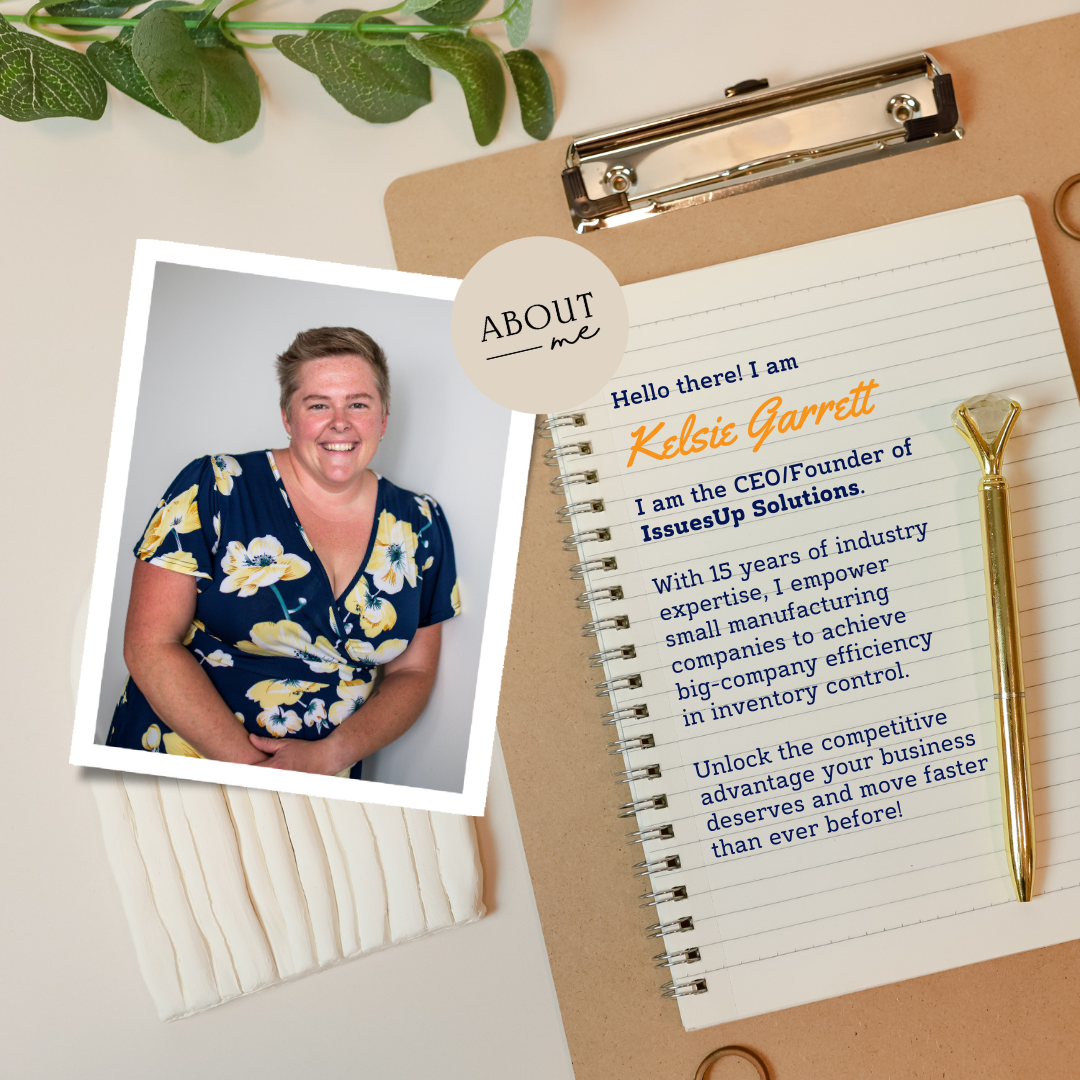